齿轮泵因结构简单、易加工、自吸能力强以及对油液污染不敏感等优点而被广泛应用于船舶、机床、国防、采矿、汽车、冶金等[1]领域。目前,国内外已开展了齿轮泵间隙[2]、泵体结构[3]、轴向间隙补偿[4]、径向压力平衡、自吸性能[5]、浮动轴套结构设计、高转速齿轮泵主动供油系统以及关于液压系统的气蚀问题及预防措施[6]等方面的研究。结果发现:齿轮泵转速越高,其吸油腔真空度越高,自吸性能越好,但随着齿轮泵转速进一步提高,由于齿廓间油液的离心运动,齿轮泵会产生一定的吸空现象,导致油液内部溶解的气体析出从而产生气穴现象。研究人员虽已对齿轮泵的真空度以及过度真空产生气穴的情况进行了研究,也为消除齿轮泵高转速工况下产生气穴提出了主动供油系统的解决方案,但对因主动供油系统产生的压力对齿轮泵轴封的可靠性没有很好的解决方案,基本上从提高轴封的耐压能力予以着手,有些耐压油封的耐压值达到了10MPa以上,但因其工作原理导致在高转速工况下极易磨损失效产生故障,从而影响主机的可靠性和齿轮泵的使用寿命。本文以外啮合齿轮泵为研究对象,阐述了齿轮泵结构特征及其工作原理,分析了齿轮泵自吸和主动供油系统工况之间的不同关系,并结合实际生产中经验积累实现了多种优化方法的分析和应用。本文为应用于一种主动供油系统的进油正压、高转速、宽温域高压力输出双联齿轮泵的优化设计。
气穴是指流动的油液在局部位置压力下降(流速高或者压力低真空)达到饱和蒸气压或空气分离压时,产生空气的分离而形成大量气泡的现象。当再次从局部低压流向高压区时,气泡破裂消失,在破裂消失过程产生局部高压和高温,出现振动和发出不规则的噪声,金属表面被氧化剥蚀,这种现象叫气穴,又叫气蚀。气穴现象的产生对主机系统有极其严重的危害性,因而必须予以采取相应的预防措施。
某些主机系统由于内部空间狭小,必须通过提高齿轮泵的工作转速以达到系统流量需求。由于高转速齿轮泵容易形成吸空,导致气穴现象发生。因而,在此类主机系统中均采用主动正压供油系统,为了保持供油的稳定性,一般设置一定的供油压力以保证齿轮泵的进油腔无低压真空现象的产生。主动供油系统原理如图1所示。
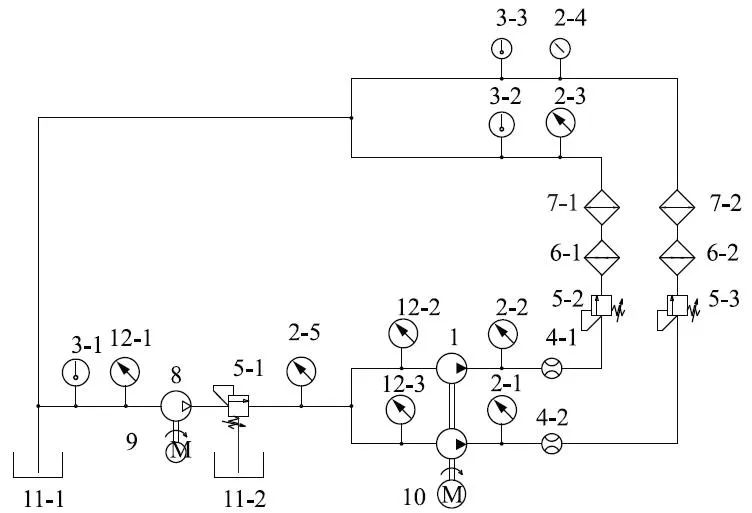
3-1、3-2、3-3.温度计 4-1、4-2.流量计5-1、5-2、5-3.溢流阀 6-1、6-2.加热器 11-1、11-2.油箱 12-1、12-2、12-3.真空表主动供油系统中,工作泵为小排量高转速齿轮泵,其进油口和增压补油泵出油口相连通,齿轮泵的旋转轴封处始终承受系统设定的补油压力,一般为2.5MPa左右。而且根据旋转油封的使用特性,在高压工况下,其允许运行转速将大幅下降。齿轮泵旋转油封装配位置典型结构如图2所示。
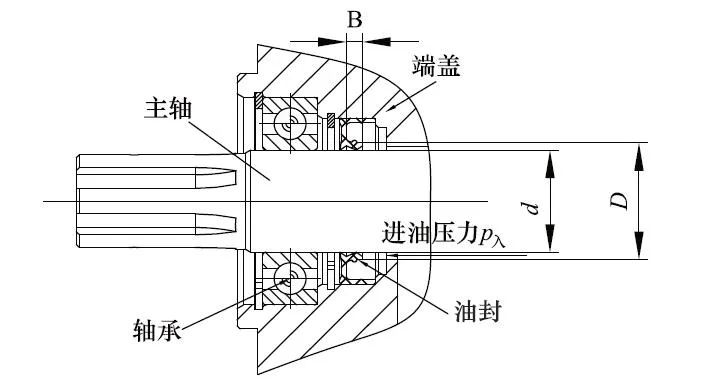
由图2所示可知,齿轮泵轴伸直径d,其工作转速为n,油封唇口承压环带直径为D,宽度为B,如果设定主轴和油封唇口的摩擦系数为μ,油封唇口处油压为p入,设定此处油封唇口弹簧力为F弹,唇口橡胶变形张力为F张,则可以得出此处摩擦副所受延径向的总法向力为:根据上述公式,我们可以得出影响油封唇口摩擦力的要素主要有三个方面,一是由轴颈粗糙度和油封唇口材料之间形成的摩擦副对应的摩擦系数μ,二是油封设计形成弹簧力F弹和橡胶变形张力为F张以及唇口结构π×D×B承压环带面积,三是油封唇口处的油液输入压力p入。常规齿轮泵在油封唇口处由于齿轮泵的自吸形成真空,因而油封唇口一般在结构上设置弹簧和一定的压缩量使其紧密贴合齿轮轴伸,此处油压一般为负值,可以忽略。因而油封唇口所受压力为唇口弹簧力和橡胶压缩变形张力之和。即:在主动供油系统中,由于供油压力的存在,油封唇口处F总因存在p入而大幅增加,在高转速工况下,此处产生大量的摩擦热能。其计算公式如下: 实际工况中,因供油压力的存在,F总大幅增加,由于高转速应用工况的需求,行程s值较常规齿轮泵大,因而在唇口将产生大量摩擦热能。由于供油压力的存在,油封唇口处的油液不能因齿轮泵自吸返回进油口,此处的热量无法有效带走产生高温,从而导致油封唇口老化(见图3)密封失效以及烧轴(见图4)等故障的发生,产品故障率高,使用寿命短。
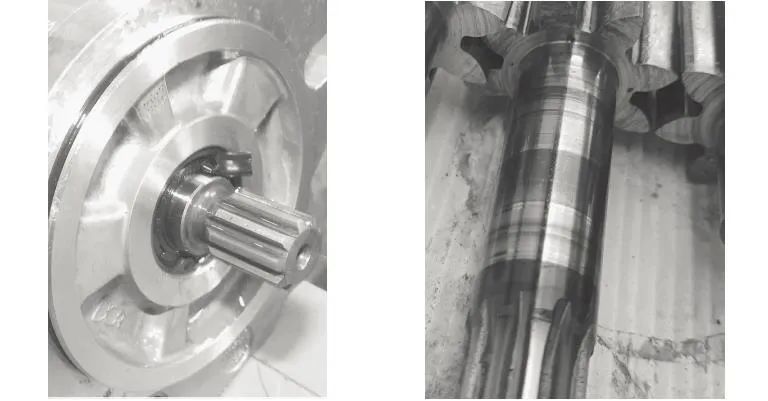
常规齿轮泵因结构适应性以及内部参数设计强度不足等问题,在实际使用中已经出现了螺栓断裂(见图5),轴套烧蚀(见图6),双联齿轮泵连接套磨损(见图7),容积效率下降过快等多种故障。为了提高齿轮泵的应用前景,要求齿轮泵需具有向宽温域(-43℃~150℃)高功率密度(高压、高速、小型化)方向发展的能力。
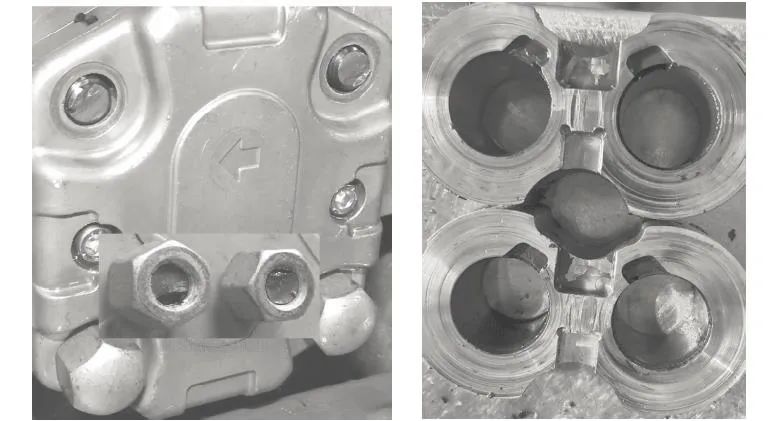
如图3~图5,产品在工作过程将产生轴封漏油、片间漏油以及不建压等影响主机使用性能或者直接造成停机等严重故障,图6、图7由于承载能力不足产生微动磨损影响产品使用寿命和可靠性。为了有效解决上述故障现象,提高产品的承载能力和使用寿命,满足特殊工况的可靠性需求,我们从产品结构,齿轮参数,材料应用等多方面予以分析解决。
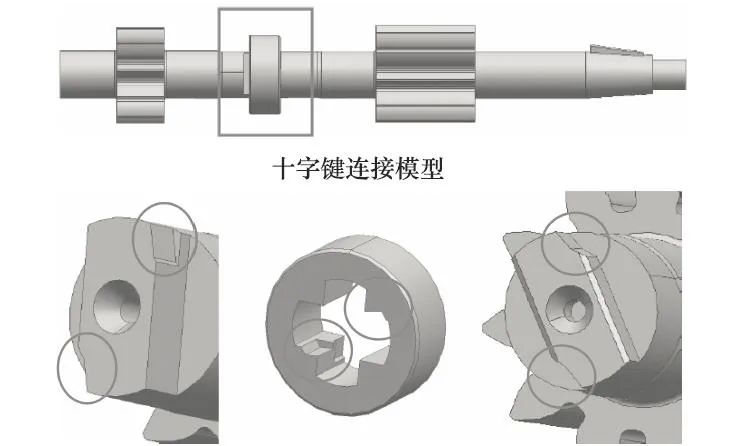
2.1 轴套采用双向密封结构设计解决齿轮泵进油腔道正压油封不承受高压问题
常规齿轮泵浮动轴套内部密封采用高、低压区分开,单旋转方向的密封方式,其进油口的压力不允许高于0.3MPa。对于齿轮泵进油腔道正压供油,当齿轮泵进油口压力为2.5MPa,这就需要油封的耐压大于2.5MPa至3MPa以上,这种方案由于进油腔道通过轴套背面回油槽处和旋转密封腔道的接通(见图8)。因而,进油腔道的压力和压力波动将直接传递到旋转油封处,对油封的要求较高,在高温、高压、高速的情况下容易产生泄漏,造成齿轮泵漏油故障,可靠性差。
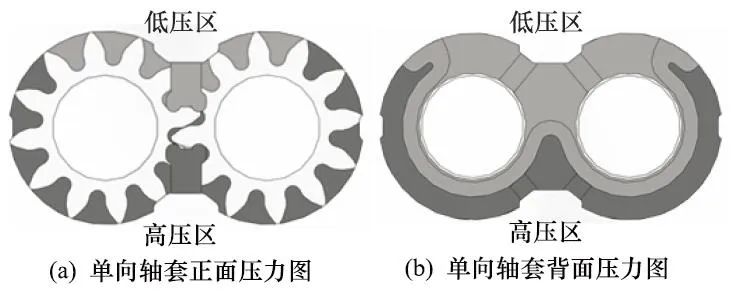
根据齿轮泵工作原理的几何模型,抽取流体域作为流体仿真计算的区域,流体域共分成三部分:入口流域、泵内齿轮传动流域以及出口流域。大致可以得到如图9所示的流线图和压力云图。
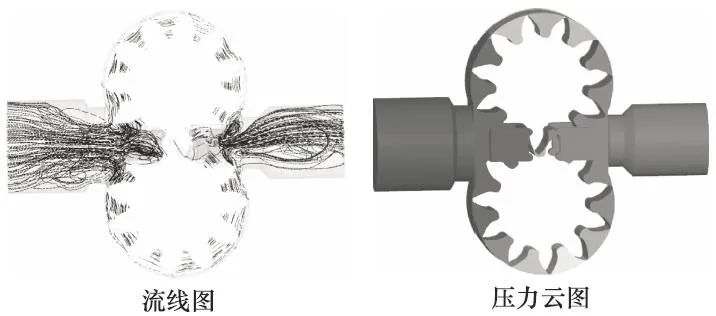
为了解决主动供油系统齿轮泵轴封的可靠性问题,采用一种双向密封结构方案,在轴套的背面将压力区分为4个区,低压区、高压区和2个次高压区(见图10),这种方案通过内部异形密封圈将齿轮泵进油腔道和旋转密封腔道隔离,进油腔道即使高压也不会对旋转密封腔造成影响,有效提高了旋转密封的可靠性,同时通过缩小高压区面积降低了浮动轴套的倾覆力矩,增加了轴套的平衡性能,降低齿轮径向液压不平衡力,改善齿轮和齿轮轴所受力情况。
2.2 增加泄油口解决高温导致的油封唇口老化、油封失效问题
后盖端增加泄漏油口结构如图11所示,充分利用产品内部循环机构的泄漏油对各重要摩擦副形成有效润滑,由高压区至低压区产生的内泄油液与泄油口的无压力形成压差,促使泄漏油的循环(如图11中的循环回油腔道),从而通过外泄形式及时将各摩擦副产生的热量充分散热、排出,也确保了齿轮泵油封处的压力和系统回油管路压力一致,不超0.5MPa,油封唇口可靠性得到大幅提高。
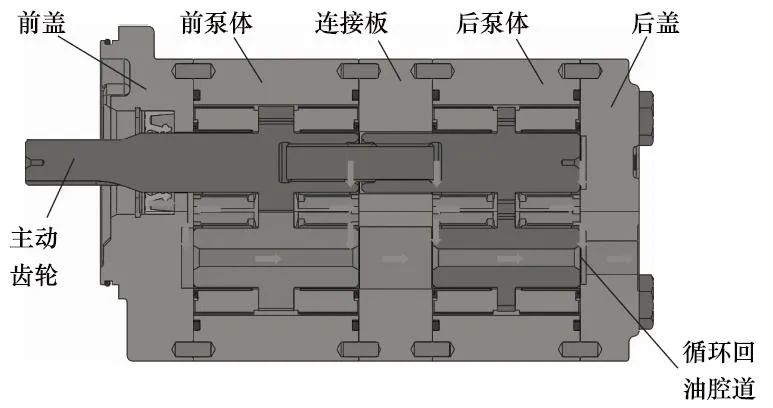
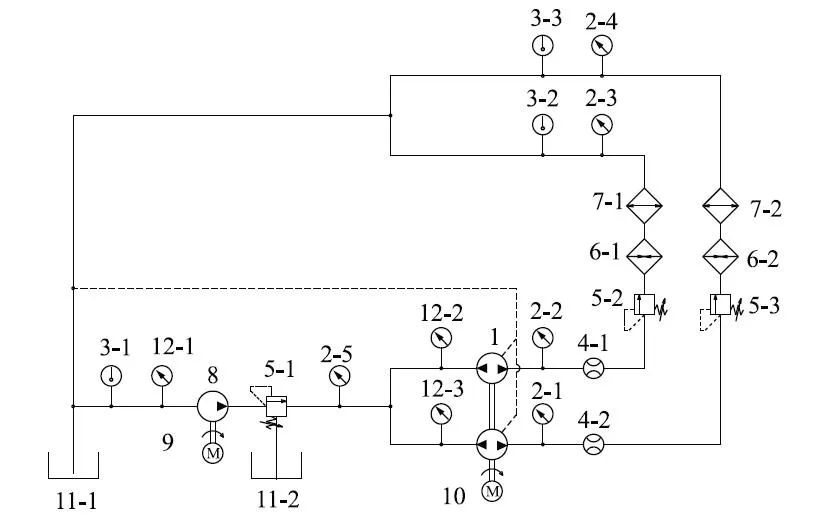
3-1、3-2、3-3.温度计 4-1、4-2.流量计5-1、5-2、5-3.溢流阀 6-1、6-2.加热器 11-1、11-2.油箱 12-1、12-2、12-3.真空表
3.1 采用五段式结构设计,缩短双联泵总体长度提高整体刚度
整体结构采用前盖、前泵体、联结板、后泵体、后盖五段式结构(如图13)。更改常规产品(如图14)的六段式双连接板十字接头连接方案(如图15)为花键轴传动单连接板(如图16)形式,有效减小齿轮泵的轴向尺寸,提高功率传输的可靠性和稳定性,切实提高了产品的功率密度水平。避免了如图7所示十字接头和连接扁键早期磨损故障的发生,提高了产品的承载能力和可靠性。
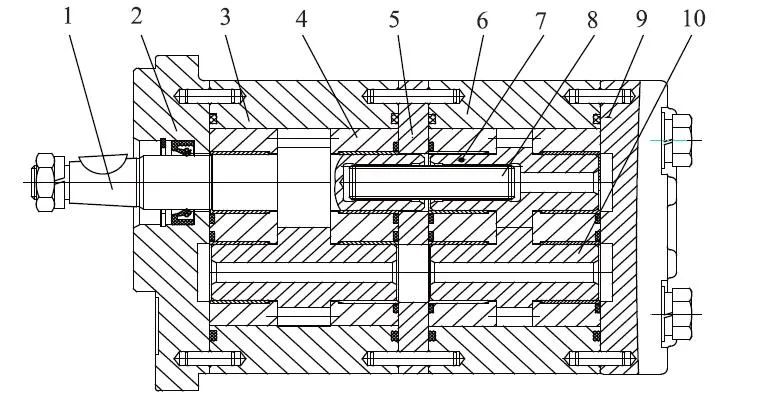
7.后泵主动齿轮 8.花键轴 9.后盖 10.从动齿轮
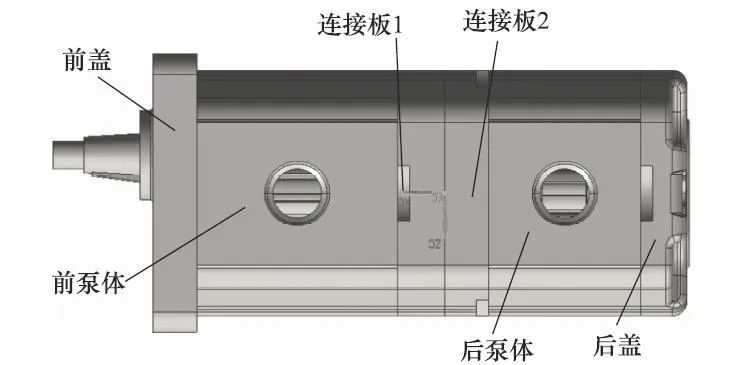
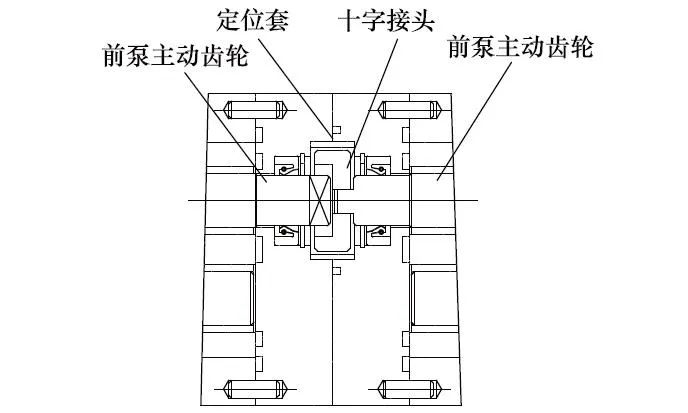
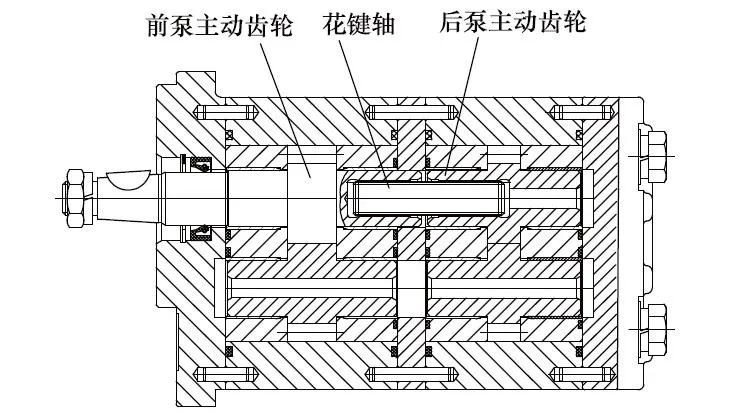
3.2 齿轮参数优化设计[7]提高承载能力,解决产品高压、高温工况下容积效率低问题采用小模数多齿双啮合齿轮参数化设计,并进行三维仿真,模拟齿轮啮合状况,确定齿轮双啮合状况最佳公法线工艺控制参数(见图17),提高齿轮的承载能力。
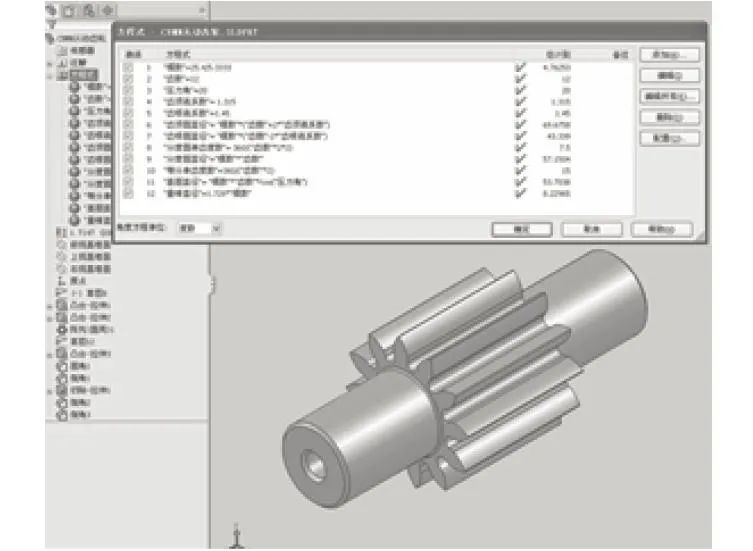
齿轮轴颈采用大模数系列产品轴颈尺寸,有效提高齿轮轴颈的抗挠度变形,增加了低温环境启动扭矩性能。齿轮采用滚、剃齿形修形工艺优化,改变齿轮齿面啮合的应力变形,有效降低齿轮啮合噪声(如图18)[8]。
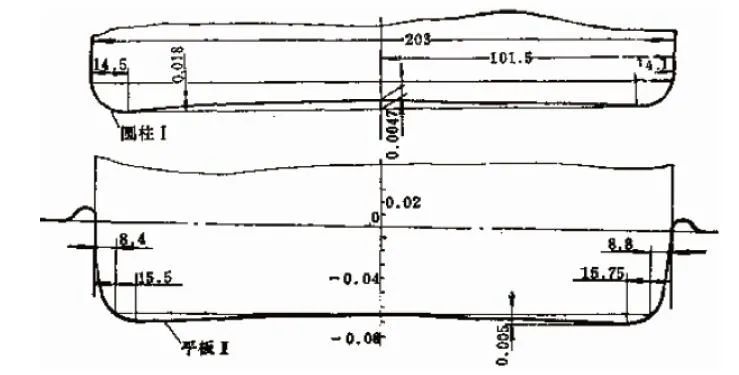
3.3 优化浮动轴套高压区设计提高产品轴向承载能力采用缩小高压区双向密封结构(如图8和图10所示)。通过对单向和双向密封结构分析,设计的齿轮泵高压、次高压、低压区域,有效降低齿轮承受的径向液压不平衡力。同时也减少了齿轮泵内部高压区面积,齿轮泵安装螺栓承受高压冲击载荷状况得到很好改善,增加了产品的整体刚度,避免出现螺栓断裂故障(如图5)。通过三维模拟齿轮双面啮合困油区间(如图19),精确计算卸荷槽尺寸,优化卸荷槽的高低温、高速、高压工况下的有效卸荷性能。
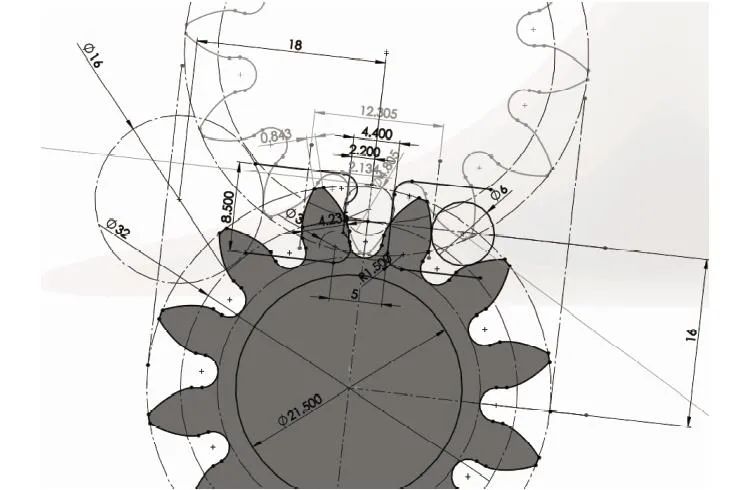
(1)采用氢化丁腈橡胶密封材料和PTFE组合油封结构设计解决宽温域工况密封有效性问题。
旋转油封采用聚四氟乙烯特制油封以及特殊的唇口设计使产品满足高转速(4000r/min)以及低温性能需求。氢化丁腈橡胶异形密封圈以及低塑性尼龙材料挡条组合式内密封结构满足产品、正压(2.5MPa)和宽温域(-45℃~150℃)使用要求。(2) 内部双向浮动轴套密封结构设计解决低温高黏度启动扭矩大以及高温低黏度内部泄漏大问题。对齿轮泵的间隙和内泄漏方面的研究,国内有很多。关于外啮合齿轮泵内泄漏理论模型的建立及参数优化[9]均有所涉及。在低温环境下,铝合金泵体、浮动轴套和合金钢齿轮由于材料特性不同,低温环境下收缩率差异较大。随着环境温度降低,齿轮泵体内壁与齿顶间间隙以及泵体厚度与齿轮厚度和浮动轴套厚度间形成的轴向间隙将逐步减小,在低温运行时齿轮旋转切割铝壳和轴套端面,不合适的间隙,造成泵体孔扫膛面以及轴套和齿轮间摩擦副面的破坏。恢复常温后,齿轮泵的容积效率将大幅下降。通过大量的试验和仿真分析,我们发现在高温时,由于油液黏度的降低,齿轮泵的内泄加大,但当随着温度的升高,齿轮泵油液黏度下降有限,泄漏量总体变化不大。原因是高温下, 油液黏度变小, 在不变的间隙下,泄漏已经达到相应的临界值,几乎接近泄漏的最大值,所以随着温度再增高,泄漏量变化不大。为了使产品具有低温工况下的启动低摩性,降低低温下油液高黏度以及摩擦副间因间隙过小导致失效的可能性,减少产品高温工况下泄漏量满足产品高温高效使用性能。结合小高压区和双向结构设计思路,通过仿真和对比试验最终确定合理的径向间隙和轴向间隙配合尺寸。并确定了三种压力区间密封区域的分布和组合密封结构内部密封形式,提高了大轴向间隙配合下齿轮泵端面密封的有效性。具体密封结构和区间划分如图20所示。
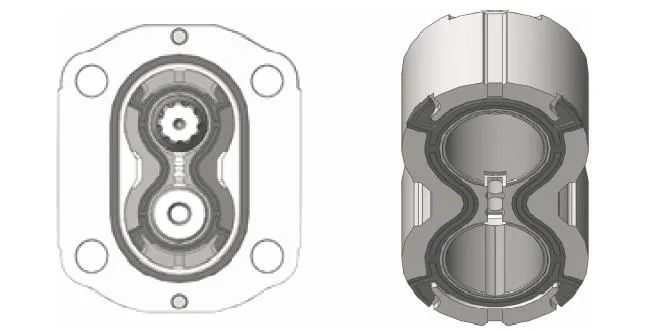
通过对主动供油系统工况以及齿轮泵内部结构的研究,综合国内外相关专业研究机构对高流速导致气穴现象发生以及高、 低温液压系统以及低摩材料方面的研究方案的综合应用。结合多年的齿轮泵生产和产品设计经验,本文很好地解决了齿轮泵的进油正压、高转速、宽温域以及高可靠性等方面性能需求问题。各项研究内容也通过产品的实际应用得到很好的验证。结合现阶段绿色电动能源的高速发展也为齿轮泵向高转速、宽温域以及与变频电机组合实现变流量控制方面的应用提供了理论和方法支撑。